The Right Accessory Saves the Day

Imagine that everything is going smoothly on a 4,600-square TPO job, and then, when work is two thirds of the way done, someone decides that the roof needs a mechanical screen.
“Things get thrown at you time and again, you have to be responsive,” says David Pope, senior project manager and estimator for Kodiak Roofing and Waterproofing, Loomis, Calif. “You have to work closely with the building owner, GC and manufacturer; come up with a solution; and make it work,” he advises.
This is part of the overall good attitude practiced at Kodiak, whose motto is: “Compromise is not an effective barrier to the elements.” The company is licensed in California (where it does the bulk of its work), Nevada, Oregon and Arizona. It specializes in single-ply and metal, and employs about 125 people at peak time. “Testimonials from satisfied customers indicate that we show concern for the client,” says President Dwayne Nash, who started the company in 1992. “We don’t just throw down the cheapest roof possible.”
The Daimler Chrysler Mopar Distribution Center, Lathrop, Calif., was a new construction project completed in late 2001. Kodiak was invited to bid because of its relationship with general contractor Walsh Construction. Kodiak had worked with Walsh on other large structures such as some Targets and Best Buys.
The system installed on the 4,600-square roof from the plywood deck up included: one layer of 1/2-inch Dens Deck, mechanically attached Firestone UltraPly® 45-mil TPO (10-foot sheets and 5-foot perimeters) and TPO-clad drip edge on the perimeter.
The job took a crew of 15 to 20 guys about five weeks, even with the surprise addition of the mechanical fence, which meant that 160 supports had to be attached. Pope explains, “Supports in some instances were very close to the edge of the roof – one side of the pitch pan was even with the outside edge of the roof.”
Kodiak worked closely with Firestone on the design of the pitch pan to make sure that the final product met Firestone’s warranty requirements. The end result was a Firestone pitch pan with a Firestone TPO-clad metal cap fabricated by Kodiak (see drawing).
“We worked together on the penetration pocket and flexible cover to find the best, most effective way to insure the warranty,” explains George Furman, contractor services division manager for Firestone Building Prodiucts. The cover had to be flexible so that when the fence moves in the wind, the sealant wouldn’t crack. Noting that Kodiak always does a great job, Foreman says it offered Firestone a certain comfort level to know that Kodiak was working on the Mopar Distribution center. “It was a big owner and an extremely unusual detail that Kodiak had to work with,” continues Furman. “They did an excellent job installing the penetration pocket, not to mention fabricating the entire piece out of TPO-clad metal.”
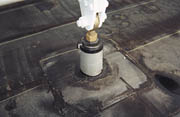
More Accessories to the Rescue!
If you have to design and build a shed to house ground-maintenance equipment including trucks with snowplows that are 26 feet wide, why not make it interesting?The architectural firm of Teng & Associates, Chicago, general contractor Castle Construction, Markham, Ill., and roofing contractor BCI Commercial Roofing, also in Markham, put together an extraordinary roof on the Ground Equipment Maintenance facility at O’Hare International Airport.
Because the snowplows are so wide, the building could not have posts on the inside. So, the over-300,000-square-foot roof actually hangs from rods that are threaded through turnbuckles and attached to bridge trusses. The support comes from concrete columns on the outside of the building.
As you might imagine, 12 rows with 40 turnbuckles each equals a flashing nightmare! Not to mention the fact that because the roof and support rods move over time, the job called for a flashing that could be readjusted and reassembled when needed. With blueprints and turnbuckles in hand, the design team turned to Portals Plus, Bensenville, Ill., for help.
The roof accessories manufacturer offered a few suggestions, and the result was a custom-made flashing based on the Portals Plus Alumi-Flash XT product. The standard product has a molded EPDM rubber cap mechanically sealed to the base with a double, weather-tight pressure seal. The flashing created for the Ground Maintenance Facility has a custom-made cap and adapter. Its retrofit cap can be unscrewed. The adapter, also made from solid rubber, is hexagon shaped to accommodate the bolt from the turnbuckle. The key to this design is that the entire product can be taken apart and put back together in order to make the necessary adjustments to the roof. Because there is movement between the base and the turnbuckle, the flashing functions as a watertight shock absorber.
So what’s the bottom line? No matter what sort of roof penetrations the job calls for, with a little time and effort, you can find the right accessory to keep the water out.
Looking for a reprint of this article?
From high-res PDFs to custom plaques, order your copy today!