Topping a State-of-the-Art Stadium
Marquee projects are a double-edged sword. Sure, high-profile jobs look great in the company's portfolio, but any mistakes made in the spotlight are magnified a thousand-fold.

Marquee projects are a double-edged sword. Sure, high-profile jobs look great in the company's portfolio, but any mistakes made in the spotlight are magnified a thousand-fold. When the job involves a stadium, the risks are even higher. Any errors, delays or overruns are not only likely to appear in the business section of the local paper, but the front page and the sports page as well.
State-of-the art projects are often the ones with minute details and unforeseen problems that can crop up when you're exploring new ground, and the degree of difficulty doesn't get much higher than the one posed by Cardinals Stadium, the new home of the NFL's Arizona Cardinals in Glendale, Ariz.
The stadium features a unique exterior design, a retractable roof, and a natural grass field that moves in and out of the stadium on a 12 million pound tray, which rides on steel rails. The field can be removed for trade shows and other events, and the grass can take advantage of the sun during nice weather so it is in optimal shape for game day, when it is moved back inside through the north wall of the stadium. Groundbreaking took place in July 2003, and the project is targeted for completion Aug. 1, 2006. The first scheduled event is an Arizona Cardinals preseason game, which will be held the weekend of Aug. 10; the first regular season game will take place Sept. 10.
The roof was a complicated job for many reasons, and so Hunt Construction Group, the general contractor on the project, was glad to team up with a familiar company, Progressive Roofing, one of the largest commercial contractors in Phoenix.

The roof system is supported by two 700-foot-long trusses that weigh about 1,800 tons, which rest on four concrete super columns. Architect Peter Eisenman's design features 21 slots in the building's metal skin and an asymmetrical roof that incorporates two retractable sections over the field, which are made of translucent Teflon-coated fabric from Birdair Co. According to Leif, major challenges during the roofing phase of the project included not only the blistering Arizona summer heat, but the roof's steep slope, the necessary fire rating and the complexities of tying in the fully-adhered membrane with the system that operates the retractable sections of the roof.
Another complicating factor for the roofing crew was a sunray pattern, which was to be made up of gray and white sections of the roof's fully adhered membrane. The design features white rays on a field of gray, and the rays are aligned with the slots in the skin. No two rays are the same size and shape, and the complex geometry of the design meant tolerances had to be exact. The membrane chosen was fully adhered 0.60 EverGuard® TPO from GAF Materials Corporation, and its standard gray and white colors were used to create the sunray pattern.

Materials could only be stacked above the completed beams, and piles had to weigh less than 900 pounds. Hawkins completed a layout indicating where everything should be placed, and all items brought up were immediately secured with nylon straps that were screwed down to metal plates. The loading was very labor intensive due to the height and the angle of the roof, Hawkins indicated. The cranes could only lift the material so far, and much of it had to be moved by hand.
The plan was to start in the southeast corner of the stadium and follow the steel erector, moving in a counterclockwise fashion and finishing in the southwest corner. "We worked from the top down in four quadrants, 50 or 100 feet at a time," said Hawkins, who designed the layout to keep the material close to its point of installation. "As much as possible, we laid it out in such a fashion that we used it as we went," he said.
Keith Feininger, safety director for Progressive, worked with Hawkins and Hunt Construction to set up the safety plan for the project. Safety lines were set up around the perimeter, and employees utilized fall protection equipment 100 percent of the time, using harnesses and lanyards on the steepest part of the roof and a guardrail system on the roof deck. Hunt had set up guardrails for the steel erectors, and these were in place as the roofing phase began. Progressive set up netting and toe boards to keep any material from rolling off of the roof surface and installed its own cable guardrail system for fall protection. "As the roofing went on, the Hunt guardrails went down and ours went up," said Feininger. "We had 30 to 40 guys there for well over six months, and we did not have an accident at that site."
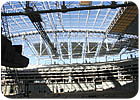
It was up to the workers from Progressive to make sure the installation of the sunray pattern was exact. "We took a line off of one of the beams straight down to the slots in the skin, then physically measured it and checked it against the computer model," said Hawkins. "We took a line of colored rope straight up into the air, then dropped it over the curved line of the roof and taped and screwed it to the deck." As each section was completed, the rope line was replaced by a chalk line to indicate the seam.
The fully adhered system posed a fire hazard during installation, as even a static charge could ignite the adhesive as it was flashing off. Extreme care was exercised at all times. Of course no smoking and no welding were permitted in the area, and 40 fire extinguishers were on hand. There were a couple of minor flare-ups due to static in the course of the installation, but these were quickly extinguished.

"This was the biggest project I had ever worked on, and we knew all eyes were on us," said Samarippas, who credited Scheele with showing him the ropes. "If we weren't on schedule, we would throw the other trades off, so we had to get it in the dry, as they say." As outdoor temperatures reached 120°, this often demanded working at night, and summer shifts started at midnight and didn't end until noon or 1 p.m. After the shift was over, Samarippas and foreman Chris Spencer would set up the lights for the next section to be completed. The halogen lights the company uses are manufactured in its own shop; the stands were strapped down or secured to anchor points at the jobsite.

The 4-foot-wide gutters were fully tied into the roof system. The 27,500 square feet of gutters around the stadium are virtually hidden from view by the skin enclosure, which curls up and over the roofline. The Progressive crews used full-tapered expanded polystyrene (EPS) insulation to create the proper slope for drainage. Then DensDeck was applied and the entire gutter system was covered with the TPO membrane.
"The keys were staying prepared and staying focused," said Samarippas. "The folks from GAF came out to check on the progress, and if there were any issues, they were right there to help us out. I'm proud to say I worked on it."
"The job was completed on time and everything looks great," said Hunt Construction's Leif. "We're 100 percent buttoned up, and the warranty is already in place. We're very pleased with the performance of Progressive Roofing and GAF. They stepped up to make sure the system met the fire rating and conducted testing to make sure we had what we needed. Hats off to both Progressive and to GAF; they both did a fantastic job."
Scheele put it all in perspective. "The most important thing was to get through it without anyone getting hurt or killed, and we did that," he said. "Safety was really the key to the whole project. It's one of the biggest jobs we've done, and everybody's happy."
Designers: Peter Eisenman, in conjunction with HOK Sport and Hunt Construction Group.
Design-Build Contractor: Hunt Construction Group, West Division, Phoenix
Roofing Contractor: Progressive Roofing, Phoenix
Owners: Arizona State Tourism and Sports Authority
Site: 28 acres in Glendale, Ariz.
Building height: 280 feet at highest point
Seating: 63,000 for football; expandable to 73,000 seats for other events
Amenities: 88 luxury suites and two 39,000-square-foot lounges.
Roofing system: 366,000 square feet of fully adhered 0.60 EverGuard® TPO from GAF Materials Corp. in gray and white
Roof board: 1⁄4-inch and 5⁄8-inch DensDeck® from Georgia-Pacific
Insulation: 31⁄2-inch Dow DeckMate™
Gutters: 27,500 square feet of gutters fully tied into the roof system
Retractable roof: Two roof panels covered with translucent Birdair fabric ride along arcing rails. Each panel weighs 1.1 million pounds. The roof opens in 12 minutes.
Grass field: The field moves in and out of the structure in a 12 million pound tray that is 234 feet wide by 400 feet long. It rolls in and out of the stadium on 13 steel rail tracks and 542 steel wheel assemblies. Seventy-six of the wheel assemblies are powered by 1-hp electric motors. It will take approximately 65 minutes for the field to travel 741 feet into position.


An artist's rendering of Cardinals Stadium (top) shows how the completed stadium will look with its rollout field in the open air. The roofing phase of the project began in May of 2005 and took approximately eight months to complete. (Photo by Diane Gola.)
State-of-the art projects are often the ones with minute details and unforeseen problems that can crop up when you're exploring new ground, and the degree of difficulty doesn't get much higher than the one posed by Cardinals Stadium, the new home of the NFL's Arizona Cardinals in Glendale, Ariz.
The stadium features a unique exterior design, a retractable roof, and a natural grass field that moves in and out of the stadium on a 12 million pound tray, which rides on steel rails. The field can be removed for trade shows and other events, and the grass can take advantage of the sun during nice weather so it is in optimal shape for game day, when it is moved back inside through the north wall of the stadium. Groundbreaking took place in July 2003, and the project is targeted for completion Aug. 1, 2006. The first scheduled event is an Arizona Cardinals preseason game, which will be held the weekend of Aug. 10; the first regular season game will take place Sept. 10.
The roof was a complicated job for many reasons, and so Hunt Construction Group, the general contractor on the project, was glad to team up with a familiar company, Progressive Roofing, one of the largest commercial contractors in Phoenix.

The Project
"It's one of the most complex buildings we've ever attempted," said Brent Leif, Design Development Manager, Hunt Construction Group, who pointed out that the moving field is the first of its kind in North America - and the only one to incorporate a system of steel wheels riding on steel tracks. The structure will be only the second NFL stadium to feature a retractable roof. Leif points out that the moving field not only minimizes humidity problems within the stadium, but it is more economical to move the field than to open and close the roof to let in sunlight.The roof system is supported by two 700-foot-long trusses that weigh about 1,800 tons, which rest on four concrete super columns. Architect Peter Eisenman's design features 21 slots in the building's metal skin and an asymmetrical roof that incorporates two retractable sections over the field, which are made of translucent Teflon-coated fabric from Birdair Co. According to Leif, major challenges during the roofing phase of the project included not only the blistering Arizona summer heat, but the roof's steep slope, the necessary fire rating and the complexities of tying in the fully-adhered membrane with the system that operates the retractable sections of the roof.
Another complicating factor for the roofing crew was a sunray pattern, which was to be made up of gray and white sections of the roof's fully adhered membrane. The design features white rays on a field of gray, and the rays are aligned with the slots in the skin. No two rays are the same size and shape, and the complex geometry of the design meant tolerances had to be exact. The membrane chosen was fully adhered 0.60 EverGuard® TPO from GAF Materials Corporation, and its standard gray and white colors were used to create the sunray pattern.

Due to the roof's steep slope, material had to be carefully loaded and immediately secured with nylon straps. (Photo by Diane Gola.)
Loading and Safety
According to Kim Hawkins, project manager, Progressive Roofing, the roofing phase of the project began on May 4, 2005. The project involved some 30 to 42 roofing mechanics working 12 hours a day, six days a week. Before work could begin, Hawkins had to determine how the material should be loaded on the roof. The loading was problematic due to the steep slope of the roof and strict weight limitations.Materials could only be stacked above the completed beams, and piles had to weigh less than 900 pounds. Hawkins completed a layout indicating where everything should be placed, and all items brought up were immediately secured with nylon straps that were screwed down to metal plates. The loading was very labor intensive due to the height and the angle of the roof, Hawkins indicated. The cranes could only lift the material so far, and much of it had to be moved by hand.
The plan was to start in the southeast corner of the stadium and follow the steel erector, moving in a counterclockwise fashion and finishing in the southwest corner. "We worked from the top down in four quadrants, 50 or 100 feet at a time," said Hawkins, who designed the layout to keep the material close to its point of installation. "As much as possible, we laid it out in such a fashion that we used it as we went," he said.
Keith Feininger, safety director for Progressive, worked with Hawkins and Hunt Construction to set up the safety plan for the project. Safety lines were set up around the perimeter, and employees utilized fall protection equipment 100 percent of the time, using harnesses and lanyards on the steepest part of the roof and a guardrail system on the roof deck. Hunt had set up guardrails for the steel erectors, and these were in place as the roofing phase began. Progressive set up netting and toe boards to keep any material from rolling off of the roof surface and installed its own cable guardrail system for fall protection. "As the roofing went on, the Hunt guardrails went down and ours went up," said Feininger. "We had 30 to 40 guys there for well over six months, and we did not have an accident at that site."
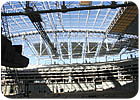
The roof system is supported by two 700-foot-long trusses, which weigh about 1,800 tons. The trusses rest on four concrete super columns.
(Photo by Diane Gola.)
The Installation
After acoustical insulation was installed in the flutes, the crew installed 31⁄2-inch Dow DeckMate™ insulation and mechanically fastened 1⁄4-inch and 5⁄8-inch Georgia-Pacific DensDeck®. The GAF EverGuard TPO membrane was fully adhered over the DensDeck in the sunray pattern.It was up to the workers from Progressive to make sure the installation of the sunray pattern was exact. "We took a line off of one of the beams straight down to the slots in the skin, then physically measured it and checked it against the computer model," said Hawkins. "We took a line of colored rope straight up into the air, then dropped it over the curved line of the roof and taped and screwed it to the deck." As each section was completed, the rope line was replaced by a chalk line to indicate the seam.
The fully adhered system posed a fire hazard during installation, as even a static charge could ignite the adhesive as it was flashing off. Extreme care was exercised at all times. Of course no smoking and no welding were permitted in the area, and 40 fire extinguishers were on hand. There were a couple of minor flare-ups due to static in the course of the installation, but these were quickly extinguished.

This aerial view of Cardinals Stadium under construction shows the completed roof system. (Photo by Todd Photographic Services.)
Beating the Heat
Progressive's Santos Samarippas began the job as a foreman and accepted a "battlefield promotion" to superintendent during the course of the project, taking over from Joe Scheele after the first few months. It was Samarippas' job to keep the project on schedule, despite the spring rainy season and the intense heat of the Arizona summer."This was the biggest project I had ever worked on, and we knew all eyes were on us," said Samarippas, who credited Scheele with showing him the ropes. "If we weren't on schedule, we would throw the other trades off, so we had to get it in the dry, as they say." As outdoor temperatures reached 120°, this often demanded working at night, and summer shifts started at midnight and didn't end until noon or 1 p.m. After the shift was over, Samarippas and foreman Chris Spencer would set up the lights for the next section to be completed. The halogen lights the company uses are manufactured in its own shop; the stands were strapped down or secured to anchor points at the jobsite.

The fully adhered roof system was tied into the retractable sections of the roof at the top of the stadium and the gutters at the perimeter. (Photo by Diane Gola.)
Details, Details
Tying in the fully-adhered system to the retractable Birdair system at the top of the roof and the gutter system at the bottom posed additional challenges. The Birdair sections were installed at the same time as the roof, said Hawkins, and the membrane was tied into the rails that hold the panels. "We ran our system up, and flashing was installed over the top," he said. GAF's TOPCOAT®, a seam-free liquid membrane system, was carefully applied around details, penetrations and pipes.The 4-foot-wide gutters were fully tied into the roof system. The 27,500 square feet of gutters around the stadium are virtually hidden from view by the skin enclosure, which curls up and over the roofline. The Progressive crews used full-tapered expanded polystyrene (EPS) insulation to create the proper slope for drainage. Then DensDeck was applied and the entire gutter system was covered with the TPO membrane.
A Job Well Done
The roofing segment of the job took about eight months, and the final details were wrapped up in March. As the finishing touches are put in place to make sure the stadium is ready to go for its first football game, the roofing crew can look back at a job well done."The keys were staying prepared and staying focused," said Samarippas. "The folks from GAF came out to check on the progress, and if there were any issues, they were right there to help us out. I'm proud to say I worked on it."
"The job was completed on time and everything looks great," said Hunt Construction's Leif. "We're 100 percent buttoned up, and the warranty is already in place. We're very pleased with the performance of Progressive Roofing and GAF. They stepped up to make sure the system met the fire rating and conducted testing to make sure we had what we needed. Hats off to both Progressive and to GAF; they both did a fantastic job."
Scheele put it all in perspective. "The most important thing was to get through it without anyone getting hurt or killed, and we did that," he said. "Safety was really the key to the whole project. It's one of the biggest jobs we've done, and everybody's happy."
SIDE BAR: Just the Facts:
Cardinals StadiumDesigners: Peter Eisenman, in conjunction with HOK Sport and Hunt Construction Group.
Design-Build Contractor: Hunt Construction Group, West Division, Phoenix
Roofing Contractor: Progressive Roofing, Phoenix
Owners: Arizona State Tourism and Sports Authority
Site: 28 acres in Glendale, Ariz.
Building height: 280 feet at highest point
Seating: 63,000 for football; expandable to 73,000 seats for other events
Amenities: 88 luxury suites and two 39,000-square-foot lounges.
Roofing system: 366,000 square feet of fully adhered 0.60 EverGuard® TPO from GAF Materials Corp. in gray and white
Roof board: 1⁄4-inch and 5⁄8-inch DensDeck® from Georgia-Pacific
Insulation: 31⁄2-inch Dow DeckMate™
Gutters: 27,500 square feet of gutters fully tied into the roof system
Retractable roof: Two roof panels covered with translucent Birdair fabric ride along arcing rails. Each panel weighs 1.1 million pounds. The roof opens in 12 minutes.
Grass field: The field moves in and out of the structure in a 12 million pound tray that is 234 feet wide by 400 feet long. It rolls in and out of the stadium on 13 steel rail tracks and 542 steel wheel assemblies. Seventy-six of the wheel assemblies are powered by 1-hp electric motors. It will take approximately 65 minutes for the field to travel 741 feet into position.
Looking for a reprint of this article?
From high-res PDFs to custom plaques, order your copy today!