Technical Details: How to Determine Proper Fasteners for Roof Applications
Recently, building owners and insurance companies have begun heightening regulations to ensure that roof systems remain in place in severe weather events. Lately, the focus has been on the number of fasteners necessary to meet geographical wind uplift requirements. The focus should also be on the type of fastener applied, as this is as critical to the success of the roof system attachment as the number of fasteners applied.

Roof attachment has become a critical issue in the industry. Fasteners gained prominence in the 1980s with the advent of Factory Mutual’s requirement of mechanical attachment to steel decks. Recently, building owners and insurance companies have begun heightening regulations to ensure that roof systems remain in place in severe weather events. Lately, the focus has been on the number of fasteners necessary to meet geographical wind uplift requirements. The focus should also be on the type of fastener applied, as this is as critical to the success of the roof system attachment as the number of fasteners applied. Proper fasteners are determined by the type of roof deck and materials required for attachment to the deck.
Prior to fastener application, a pullout test should be performed in accordance with ANSI FX1 to determine the deck’s ability to hold the fastener and the type of fastener required for optimum attachment. A pullout test is performed by driving a fastener into the deck and leaving enough room to attach the pullout tester to the fastener head. The tester is then used to pull the fastener out of the deck. The force necessary to pull the fastener out of the deck is recorded. The pull force required is typically determined prior to the test. If the fastener meets the required pressures then its use - with that deck type - is approved. A minimum of 10 pullout tests should be completed in each roof area with the average of the tests used as the pull force.
No matter what types of deck or materials are applied, the fastener used should be corrosion resistant. Most fasteners currently used in the roofing industry are corrosion resistant. The most common type of fasteners on the market today are carbon steel fasteners with electro deposition epoxy coatings. The epoxy coatings have replaced the old fluorocarbon coatings. Stainless steel fasteners are available for specialty applications in highly corrosive conditions. Corrosion resistance is required due to the level of moisture encountered in roof systems. Moisture contact with non-corrosion-resistant fasteners leads to fastener corrosion throughout the shank and subsequent attachment failure.
Proper fastener selection should be based on the following criteria:
• Deck.
• Materials.
• Overall length.
• Nature of drill point.
• Thread design.
• Stress plate and fastener head.
Fastener selection is predicated on the type of deck and the type of materials required for attachment. Each deck type has specific fasteners required for use. The types of materials that are to be attached also provide consideration. The most important issue regarding material application is that the fastener is long enough to properly secure the material and penetrate the deck. Penetration depth differs by deck type. For steel decks the depth should be a minimum of 3⁄4 of an inch, for concrete decks and wood plank decks it should be minimum 1 inch, and for plywood, 1⁄2 inch. The contractor should check with the fastener manufacturer for depth on specialty decks such as lightweight, tectum and gypsum. The fastener manufacturer should be consulted to determine the best type of fastener to be used under each specific condition.
The most common problem associated with fasteners is fastener back-out. This condition weakens the fastener’s anchorage capacity and increases the probability of roof damage from blow-off or excessive movement. Fastener back-out can be avoided through the use of proper application methods and through proper fastener selection. The physical properties such as overall length, nature of drill point, thread design, stress head and fastener plate must be taken into consideration. Oftentimes, fastener back-out is mistakenly identified in cases of pop-out that occurs from wet or compressed insulation.
Overall length is an important criterion, particularly in recover applications, where the fastener can be more than 6 inches in length. There is a direct correlation between the fastener’s holding power and the overall size. Research has indicated that long fastener shanks provide longer levers to dislodge the fasteners from the anchorage points. The fastener’s flexural strength diminishes as the size of the shank increases. Typically, fastener back-out is created through a combination of system movement and vibrations that rock fasteners back and forth and enlarge the thread opening. Shorter lengths are preferable when possible.
Drill points on self-drilling fasteners can be either extruding or cutting points. Extruding drill points push the displaced metal or wood aside through reliance on heat (friction). On the other hand, cutting drill points lift the removed metal or wood from the hole. The drill point that provides the best pullout value and back-out resistance is one that produces a small hole and the deck is fastened through the threads.
Fastener thread design has improved in recent years through the reduction of the top slope with the threads, which is the angle of the shank in correlation to the horizontal head. This design has provided a higher stripping torque and reduced the risk of fastener blackout. Another recent advancement has been through the use of plastic stress plates and round steel plates. Plastic stress plates and round plates can prevent the cutting punctures that can occur with steel stress plates when the fasteners are overdriven, leaving the steel ends in a vertical state.
Installation techniques are as critical as fastener selection. The fastener can only provide proper holding power if it is attached in the required manner. The most common installation errors are overdriving or underdriving the fastener into the substrate. Problems also occur when the fasteners are driven at angles other than the required 90 degrees, leaving fasteners at angles and not fully driven into the substrate. These conditions lead to back-out of fasteners, which weakens fastener anchorage and can lead to membrane punctures. All fasteners that have been improperly applied should be removed.
A common installation error in fastening of insulation to the deck occurs when the fasteners are applied too close to the edge of the insulation boards. For best results, the fasteners should be applied a minimum of 6 inches from the sides of the insulation.

Roof attachment has become a critical issue in the industry. Fasteners gained prominence in the 1980s with the advent of Factory Mutual’s requirement of mechanical attachment to steel decks. Recently, building owners and insurance companies have begun heightening regulations to ensure that roof systems remain in place in severe weather events. Lately, the focus has been on the number of fasteners necessary to meet geographical wind uplift requirements. The focus should also be on the type of fastener applied, as this is as critical to the success of the roof system attachment as the number of fasteners applied. Proper fasteners are determined by the type of roof deck and materials required for attachment to the deck.
Prior to fastener application, a pullout test should be performed in accordance with ANSI FX1 to determine the deck’s ability to hold the fastener and the type of fastener required for optimum attachment. A pullout test is performed by driving a fastener into the deck and leaving enough room to attach the pullout tester to the fastener head. The tester is then used to pull the fastener out of the deck. The force necessary to pull the fastener out of the deck is recorded. The pull force required is typically determined prior to the test. If the fastener meets the required pressures then its use - with that deck type - is approved. A minimum of 10 pullout tests should be completed in each roof area with the average of the tests used as the pull force.
No matter what types of deck or materials are applied, the fastener used should be corrosion resistant. Most fasteners currently used in the roofing industry are corrosion resistant. The most common type of fasteners on the market today are carbon steel fasteners with electro deposition epoxy coatings. The epoxy coatings have replaced the old fluorocarbon coatings. Stainless steel fasteners are available for specialty applications in highly corrosive conditions. Corrosion resistance is required due to the level of moisture encountered in roof systems. Moisture contact with non-corrosion-resistant fasteners leads to fastener corrosion throughout the shank and subsequent attachment failure.
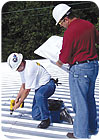
Fasteners should be selected based on the type of roof deck. (Photo courtesy of Triangle Fastener Corp.)
• Deck.
• Materials.
• Overall length.
• Nature of drill point.
• Thread design.
• Stress plate and fastener head.
Fastener selection is predicated on the type of deck and the type of materials required for attachment. Each deck type has specific fasteners required for use. The types of materials that are to be attached also provide consideration. The most important issue regarding material application is that the fastener is long enough to properly secure the material and penetrate the deck. Penetration depth differs by deck type. For steel decks the depth should be a minimum of 3⁄4 of an inch, for concrete decks and wood plank decks it should be minimum 1 inch, and for plywood, 1⁄2 inch. The contractor should check with the fastener manufacturer for depth on specialty decks such as lightweight, tectum and gypsum. The fastener manufacturer should be consulted to determine the best type of fastener to be used under each specific condition.
The most common problem associated with fasteners is fastener back-out. This condition weakens the fastener’s anchorage capacity and increases the probability of roof damage from blow-off or excessive movement. Fastener back-out can be avoided through the use of proper application methods and through proper fastener selection. The physical properties such as overall length, nature of drill point, thread design, stress head and fastener plate must be taken into consideration. Oftentimes, fastener back-out is mistakenly identified in cases of pop-out that occurs from wet or compressed insulation.
Overall length is an important criterion, particularly in recover applications, where the fastener can be more than 6 inches in length. There is a direct correlation between the fastener’s holding power and the overall size. Research has indicated that long fastener shanks provide longer levers to dislodge the fasteners from the anchorage points. The fastener’s flexural strength diminishes as the size of the shank increases. Typically, fastener back-out is created through a combination of system movement and vibrations that rock fasteners back and forth and enlarge the thread opening. Shorter lengths are preferable when possible.
Drill points on self-drilling fasteners can be either extruding or cutting points. Extruding drill points push the displaced metal or wood aside through reliance on heat (friction). On the other hand, cutting drill points lift the removed metal or wood from the hole. The drill point that provides the best pullout value and back-out resistance is one that produces a small hole and the deck is fastened through the threads.
Fastener thread design has improved in recent years through the reduction of the top slope with the threads, which is the angle of the shank in correlation to the horizontal head. This design has provided a higher stripping torque and reduced the risk of fastener blackout. Another recent advancement has been through the use of plastic stress plates and round steel plates. Plastic stress plates and round plates can prevent the cutting punctures that can occur with steel stress plates when the fasteners are overdriven, leaving the steel ends in a vertical state.
Installation techniques are as critical as fastener selection. The fastener can only provide proper holding power if it is attached in the required manner. The most common installation errors are overdriving or underdriving the fastener into the substrate. Problems also occur when the fasteners are driven at angles other than the required 90 degrees, leaving fasteners at angles and not fully driven into the substrate. These conditions lead to back-out of fasteners, which weakens fastener anchorage and can lead to membrane punctures. All fasteners that have been improperly applied should be removed.
A common installation error in fastening of insulation to the deck occurs when the fasteners are applied too close to the edge of the insulation boards. For best results, the fasteners should be applied a minimum of 6 inches from the sides of the insulation.
Looking for a reprint of this article?
From high-res PDFs to custom plaques, order your copy today!