
A worker installs decorative stamped pieces as
the project nears completion. The initial phase of construction is shown below. (Photos courtesy of Commercial
Construction Services.)
When a fire in the historic section of Hoboken, N.J., destroyed the ornate copper eaves and cornice of a century-old building, restoring it to its former glory seemed almost impossible. One contractor thought it could be done: Brian David Goe, President of Commercial Construction Services in Edgewater, N.J.
The company, which has been in business since 1982, installs commercial roof systems and does custom sheet metal design and fabrication, exterior waterproofing, and all phases of masonry restoration. It also designs and installs solar systems. But its real specialty is commercial and institutional restoration and retrofit work.
“There are not many challenges with new construction, especially in our trade,” said Goe. “The real challenges come from restorative and retrofit work, all of which tests your skills, experience and ingenuity at a higher level.”
Goe became interested in restoration and construction at an early age. “I was encouraged and inspired by a contractor neighbor of mine when I was 12 years old,” he recalled. “It was a good way for me to stay out of trouble and to preoccupy my time and learn a trade after school and on weekends and during summer recess. As a young boy I recall watching my neighbor, who was like Norm Abram of ‘This Old House.’ He was always repairing, restoring or building something on his home in a very professional, skillful and meticulous manner.”

Intricate Details
Twenty-eight years after founding his company, Goe would find the Hudson Street cornice project would be the supreme test of his company’s restoration skills. “We were invited to bid on the project since we have serviced Applied Housing in the past,” he said. “They own many old buildings like this in Hoboken and surrounding towns.”Fire apparently had broken out in one of the condominium units on the fifth floor - the top story. Damage was extensive, and the ornate copper work at the rooftop was almost completely destroyed.
Not only was the restoration work intricately detailed, but it was imperative for the owner to get the building’s occupants back into their condos as quickly as possible. “The project began in the heart of winter with a tight schedule to complete both the interior rebuilding and the exterior restorative process,” Goe said. “Clearly the building owner wanted to obtain a C/O (certificate of occupancy) as soon as possible so that the residents could return to their homes.”

The pre-planning process involved several site meetings with the lead fabricator, shop drawings, and the fabrication of samples of each component. “Once the templates were done, we field tested the samples to ensure all of the components lined up and matched the existing profiles to near perfection, since the objective was to replicate the craftsmanship and profile of this near-century-old building,” Goe noted.
After the templates were completed and the mock versions were double-checked in the field, the company began to rebuild the intricate wood framing and support members located behind the cornice work. “Each and every point was shot with a laser beam to establish plumb lines while tying into the old framing work,” he said. “At times we tend to get technical, as this ensures accuracy and prevents delays while tinkering and toying with the tie-ins while aligning all of the components. Certainly you don’t want to have to disassemble the delicate copper cornices once they are cut, fit and installed.”
Once the carpentry work was complete, the next step was to custom fabricate new brackets from hardened copper bars. “We had to brake form the bar to match the profile of the cornice and soffit, which was originally designed to support the shell of the copper soffit,” Goe said.

“In all there were 10 separate components to make up a complete section of cornice, soffit and fascia,” Goe said. “One of the most challenging aspects of the project was mitering each piece - particularly since there were varying circumferences on each section of the copper cornice and dental. Furthermore many of the existing angles were not your ordinary 22- or 45-degree angles.”
For areas with original pieces of copper that could be restored, the company used sheets of a Revere Patina green copper. The company uses a proprietary process to oxidize the copper, allowing it to closely match the portions of the original cornice work that could be salvaged. “We used the Patina copper to replicate some of the damaged copper dental and fascia,” he said. “Although where we had to gut out and remove the entire cornice and soffit work we used a 20-ounce Revere red copper. Unfortunately for stamping purposes, the Revere Patina green copper does not stamp as well. The process in which Revere applies the patented Patina green surfacing hardens and stiffens the copper sheets. This in turn prevents the intricate details being stamped from appearing on the intricate and stamped floral components.”
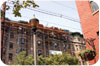
After the cornice was completed, the final phase of the project involved restoring and cleaning the fire-damaged brick, lintels and limestone windowsills. “We used various masonry restorative cleaners from Prosoco, which has a great line of restorative products to remove soot, black smoke and carbon from porous masonry surfaces,” said Goe. “They are gentle enough for old surfaces. Lastly we had to re-point the top shelf of the brick facade.”
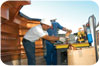
Challenging Conditions
The cold temperatures and the wind off of the Hudson River were major challenges, and the schedule was further complicated by 21 days of rain in a single month. “The weather slowed us up considerably,” Goe said. “Working in the single-digit temps, especially with the harsh wind off of the Hudson, made it all the harder to be productive. Especially when performing very intricate and tedious work, you more or less ‘freeze up’ and become numb while standing in one place on a scaffold 70 feet up in the air for eight hours in a day. It’s really not all that fun.”Goe reiterated that the biggest challenge on the project was the mitering of the outside and inside corners. “Our primary master mechanic, Claudio Leal, worked tirelessly on the job,” he said. “He did an impressive job. There aren’t many skilled men out there who can do this type of work, and we want to maintain it and do quality work to keep that sector of the industry alive.”
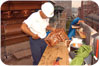
Other high-profile projects the company has worked on include The Central building at Seton Hall University, Saint Patrick’s Cathedral, Landmark building at Stevens Institute of Technology and many others.
“We believe our diverse background, and we like to think of ourselves as the ‘Jack of all trades - master of all,’” Goe said. “We developed divisions that specialize in the maintaining and restoring the exterior building envelope. Were basically one-stop shopping for the architectural preservation firms we service.”
Goe cites the company’s highly trained tradesman and the focus of its four in-house divisions as keys to his company’s success.
“We’re one of the few that do what we do, and we take pride in those finer details,” he said. “We’ve been at it for 28 years, and we’re the biggest perfectionists we can be.”
For more information on the company, visit www.commercialconstructionservices.net.