Technical Details: Drainage Requirements
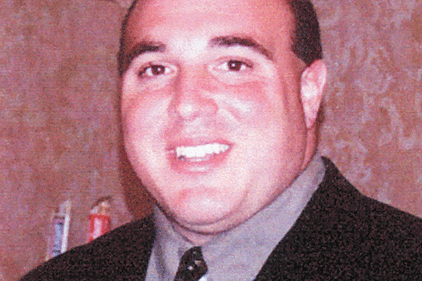
The detriments of standing water on the roof surface are well documented and quite extensive. The severity of the defects ranges from structural damage and membrane degradation to temperature changes and the growth of vegetation and fungi. Standing water is such a deterrent that most low-slope roof system manufacturers require that the roof surface is free of all rain water within a specified period of time for their warranties to be valid.
The most serious defect of standing water on the roof surface is structural damage. Structural damage can occur if water is allowed to pond in large areas for any length of time. Standing water can be deceptively heavy, and if the added weight of the water causes the roof to exceed the design load, the roof could collapse.
Structural damage is the most extreme and least common effect of standing water. A more common problem is membrane degradation. Standing water can leach oil from bitumen in asphalt-based BUR systems and decreases mil thickness in single-ply assemblies. Once the membrane has been reduced to a vulnerable stage, the possibility of moisture penetrating into the system increases — especially at the site of imperfections such as fishmouths, splits, bare felts, open seams and unsealed felt laps. Once moisture has entered into the system it never completely dries; wet insulation will deteriorate over time and can contribute to premature system failure. Moisture in the system also detracts from the insulation’s thermal and structural integrity, and can result deck damage.
Slope Requirements
When designing a roof system that allows for the proper drainage of accumulated moisture, the designer should take a number of conditions into account. There is no one slope that will provide for proper drainage on all roof systems. Particular consideration must be applied to the structural framing of the roof, the deck type, the roof membrane specification and the building layout.
The slope can be provided through primary means — such as slope in the deck — or through secondary means. Positive slope in the structure at a rate of 1/4inch per foot to 1/2inch per foot is required, depending on the installed roof system. The recommended minimal slope for aggregate surfaced systems is 1/4inch per foot. The 1/4-inch-per-foot slope is acceptable because there are many building industry imperfections and this measurement contains a tolerance for them. A smooth surfaced roof system warrants a 1/2-inch per foot slope.
Deck deflection and drain placement are also important considerations when determining roof slope. The deck deflection must be limited to no more than 1/240 of the roof span. This is of critical importance to accommodate the stress of either concentrated or uniform loading. Drains should always be located at the mid span because these are the points of maximum deflection. Therefore, if the deck span is 50 feet, the deflection should not be more than 21/2inches (1/240 of 50 feet).
Placing drains at points of minimum deflections, such as columns or bearing walls, should be avoided due to loading conditions. However, if it is required that drains are placed at columns or bearing walls, the slope of the roof must be increased. Increasing the slope will compensate for the minimal deflections in these areas. The allowable deflection will remain 21/2inches, but an additional 5 inches of roof slope must be provided to keep the deck level at the mid span under maximum loading conditions.
Types of Drainage Systems
There are two types of drainage systems for a low-slope roof: a peripheral drainage system and an interior drainage system. The designer must determine the drainage system that is best suited for the roof system, the building layout and the climate.
In a peripheral drainage system the slope is designed to allow drainage from elevated interior areas to peripheral low points. Accumulated moisture is eliminated through scuppers and leaders located outside of the building. In mild climates where winter temperatures remain above freezing the peripheral drainage system has been effective. However, in colder climates ice and snow can hinder the flow of moisture. The peripheral drainage system also requires more elaborate flashings to protect the gutter and scupper areas from erosion. These areas are also more vulnerable to ice damming and metal distortion from freeze-thaw cycles.
In the interior drainage system, accumulated moisture flows from elevated peripheral areas to interior roof drains. The water flows through a leader, which conducts the water through the interior of the building. The leader is connected to columns the majority of the time. The most distinct advantage of this system is that because the drainpipes are located on the building’s interior they are constantly heated. This allows the rainwater or melting snow to flow through the system throughout the entire year.
Drainage Requirements
Once the drainage system is determined, the designer must ensure positive drainage by correctly positioning the roof drains. A good rule to follow is to provide two roof drains for a total roof area less than 10,000 square feet. An additional roof drain should be added for each 10,000-square-foot area. The drains should be placed at a maximum of 75 feet in each direction away from each other. The only exceptions would be drains that are placed around obstructions, such as penthouses, HVAC equipment, skylights or other similar penetrations. Drains should be placed in these areas because water does not have the ability to turn corners in an effort to flow to the drain.
The most dependable type of roof drainage design is the inverted pyramid pattern. This type of pattern is particularly useful on buildings that are easily divided into rectangular areas. The premise of the pattern is that a drain is positioned in the center of the rectangular area and there is a four-way positive slope into the drain. Tapered insulation could be used to create this type of slope or it could be field built with roof framing systems such as wood, cast in place or lightweight concrete.
The roof drain should be recessed below the roof surface. This can be accomplished by setting the head of the roof drain below the insulation level and by providing a sump at the drain. Tapered insulation panels should be installed around the drain to ensure positive flow of water towards the drain. The tapered insulation also serves as prevention against condensation.
Interior Drainage
Proper interior drain design for low-slope roof systems is determined through a calculation of site-specific factors. The calculation to determine the number of primary drains that are required for a specific roof section requires four criteria: the slope of the roof area, the size of the deck area, the size of any adjacent areas that contribute flow to the area, and the height of the perimeter parapet wall (if installed). Local codes and rain intensity levels for the area should also be considered in the determination.
The drains should be designed to accommodate the hydraulic head of 4 inches of total depth of ponding. This may require the installation of overflow drains or scuppers, which also may be necessary for code compliance. Interior overflow drains should be set at the distance allotted by code and should always be on a separate horizontal line. Overflow drains are required as secondary drainage if the primary drainage is blocked or overloaded. Installing overflow drains to the same lines will eliminate flow due to the primary drains constraints.
Scuppers can also be provided as primary or secondary drainage points. Scuppers are rectangular openings in parapet walls that are a minimum of 4 inches in width and height ranging from 4 to 6 inches. If the scuppers are used as primary drainage, then they are applied flush with the roof level. If they are used for secondary drainage, then they should be a minimum of 2 inches above the roof level and a maximum of 4 inches above the roof level.
Once the number of required drains for the area is determined, the size of the drain inserts and plumbing should be established. This is completed using a plumbing calculation. The calculation utilizes data from the rainfall map that shows the maximum rainfall in inches per hour throughout the United States. Step one is to determine the rate based on the geographic location of the building.
Step two is to change the data from inches per hour to gallons per minute (GPM), which is the designation used for plumbing pipes and drains. Use the chart entitled “Rainfall Conversion Data” to determine the GPM per 1 square foot. Once this number is derived, multiply it by the total square footage of the drainage area to determine the gallons per minute (GPM).
The determination of the drain sizing and horizontal pipes is based on information found in the “Sizing System Data Chart”. For roof drain size, the flow in GPM is compared to the column on the chart entitled Roof Drain and Vertical Leaders. The flow rate from the drain must equal or exceed the GPM from the chart. Horizontal drainpipe sizing use the rates based on slope in the chart. Water does not flow at an equal rate based on slope. The steeper the slope, the greater the rate of flow.
Drainage Details
Adequate deck slope, efficient deck deflection and the proper placement of drains are major attributes of successful roof drainage systems. However, there are a number of design details that can cause problems.
Drains should not be placed near base flashings. The water that builds up around the drains exposes the flashing seams and could be a source of moisture intrusion into the system. Base flashings should always be located at high points to prevent water from building up around them. Drains should always be located at low points, a relatively logical concept that is not always adhered to. When a situation arises where a drain must be placed in a flashing area, around a unit or curb, crickets should be considered.
The roof drain area is vulnerable to moisture penetration because of the constant water buildup. The drainage area is the second most common area for roof leaks. Due to this fact, corrective actions should be taken to guard against moisture penetration. The membrane plies should extend to the inside of the roof drain bowl ring to secure proper coverage in this area. Drain detail should be completed in accordance with the membrane manufacturer’s requirements.
The best way to guard against leaks at the drainage areas is to accommodate for differential movement between the drain and the roof deck. The roof system must have the ability to move as a unit. This requires strong securement of the roof drain to the roof deck. Secure the drain ring over the completed membrane. This will prevent wind uplift. The drainpipes need to be flexible enough to move in all directions, so that there if there is any type of movement in the drains the pipe will move with it.
A common cause of drainage failure is the accumulation of debris that enters the drain and causes a system backup. This can be prevented by securing a strainer over the drain. Annual maintenance inspections should be conducted to make sure drains are free-flowing and not clogged with debris.
The best way to avoid drainage debris on aggregate or ballasted surfaced systems is to install a gravel stop around the drainage area. A 1-foot-by 4-inch gravel stop fabricated from .032 mil finish aluminum or 16 ounce copper should be secured to the membrane surface at a minimum 3-foot diameter around the drain.
Looking for a reprint of this article?
From high-res PDFs to custom plaques, order your copy today!