On the Prowl with Cougar Paws SteelWalker Boots
SteelWalker boots dominate metal roofing market down under, and are making their way to the U.S.
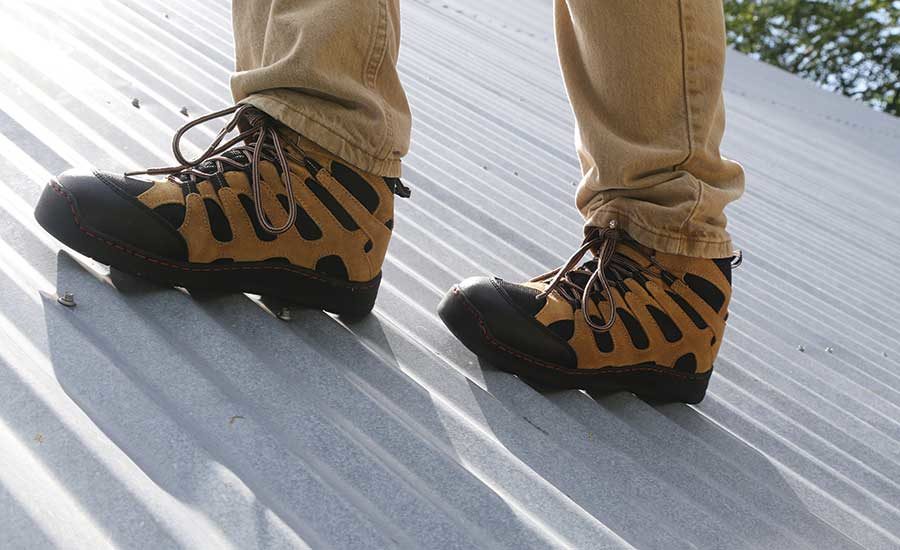
I was first introduced to Cougar Paws® boots in the winter of 1999 at the first Northeast Roofing Contractors Association (NERCA) Convention in Boston.

I was first introduced to Cougar Paws® boots in the winter of 1999 at the first Northeast Roofing Contractors Association (NERCA) Convention in Boston.

I was first introduced to Cougar Paws® boots in the winter of 1999 at the first Northeast Roofing Contractors Association (NERCA) Convention in Boston.

I was first introduced to Cougar Paws® boots in the winter of 1999 at the first Northeast Roofing Contractors Association (NERCA) Convention in Boston.




I was first introduced to Cougar Paws® boots in the winter of 1999 at the first Northeast Roofing Contractors Association (NERCA) Convention in Boston. Since then, I’ve tested, worn and written about Cougar Paws boots several times for RC. Last year, Dan Cougar, owner and CEO, contacted me to conduct further static load performance tests on a newly-designed roofing boot with magnetic soles. A year before that, Cougar’s company entered into a licensing agreement with Ben Donaldson, founder of M-Roofer Magnetic Roofing Shoes Co., a patent holder based in Merewether, Australia. Donaldson invented, designed and manufactured an excellent roofing shoe for the low pitch roofs in Australia, where steel roofing dominates the market. Soon thereafter, Cougar Paws began further research and development of an 8-inch high leather roofing boot using Donaldson’s patented magnetic design, specifically for the steep pitch steel roofing and ironworking trades in North America.
The original Cougar Paws became the only boots I wear while roofing or conducting elevated training exercises. Although the manufacturer no longer recommends it, until recently I used these boots with replaceable rubber pads for years while accessing both steel and aluminum roof panels on my own home and outbuildings. The micro pores within the pad’s rubber compound are the key to the superior adhesion on most types of roofing, hence my nickname “Glue Shoes.”
Over time, small particles of the outer rubber are removed by natural abrasion from the mineral or wood shingle surfaces, and a new layer of the micro-perforated compound is revealed below. The inexpensive, consumable Velcro-mounted pads are meant to be periodically replaced before advanced erosion.
Dan and I both noticed years ago that working as little as a day or two on metal the original pads became less effective. Instead of being naturally abraded, the pores in these replaceable pads would become clogged with fine construction dust and debris, eventually leading to less traction. The slow erosion of the outer layer of the replaceable pad caused by the abrasive mineral surface of shingles, does not occur on metal roofing. Without refreshing a new contact surface, metal particles on older roofs or other substances would accumulate in the pores of the pads and eventually lose traction. I built a plywood scuff-board with several asphalt shingles attached and set it up with a folding chair near the bottom of the roof’s access ladder. Stopping to scuff the pads every time before ascending or descending the access ladder further extended the function of the pads while working on metal. But, the recent advent of the Cougar Paws SteelWalker® mag-boot would soon change everything.
Galvalume® roofing was first produced by U.S. Bethlehem Steel in 1972 by hot dipping steel coils with an alloy of 55 percent aluminum and 45 percent zinc. Today it’s the top steel roofing product on the market. In 2008, the BIEC International Inc., the worldwide licensor for the product, estimated more than 100 million tons of Galvalume have been manufactured — enough to cover more than 80 billion square feet of roofs around the world. A decade later the numbers have exploded, making Galvalume synonymous with metal roofing.
Metal Roof Field Trial
Last summer, I provided six pairs of standard Cougar Paws boots with replaceable pads to a local roofing contractor about to install 36 squares of clear-coated Galvalume panels on a 10:12 pitch roof with multiple gables, dormers and valleys. The summer heat required an early morning start, but heavy dew condensed on the metal overnight prevented it. The foreman said once he and his crew made access, they performed “like pigs on ice.” No matter what footwear the crew tried either standing or walking in wet or dry conditions, there were continuous falls-in-place despite using personal fall arrest systems (PFAS). They began roof work after the dew had evaporated but soon resorted to using alcohol-saturated pad mops to accelerate the drying and cleaning process. They eventually devised a complex, site-specific system of horizontal and vertical lifelines, latex rubber knee pads, nitrile-coated gloves and bathmats in order to maximize traction and grip. Ultimately, installation of Galvalume required the implementation of multiple roof ladders (wood to avoid scratches) and horizontal/vertical lifelines while wearing specialized FP harnesses. There were some locations around valleys and dormers where nothing but “dangling from ropes” proved effective. The contractor eventually rented a much larger, aerial work platform with an articulated boom to deliver sheets directly to crews from the ground. Crew members eventually became adept at sitting side-saddle on the deck and adjusting their suspended bosun’s seats with tie-back lines, but the real problem remained moving point-to-point on a 10:12 pitch while handling 16 ft. x 3 ft. steel panels. It was awkward, exhausting, time-consuming and potentially dangerous. At the end of the job, the contractor compared his actual labor and equipment costs to his original estimate, and discovered a cost overrun approaching 90 percent.
Once installed, the Galvalume roof certainly has many impressive value-added features, boasting an average manufacturer’s warrantee of 20-25 years. With adequate preventative maintenance and care it can provide a potential lifetime almost twice that long. But installation of the product is anything but a cakewalk.
Anatomy Of Adherence
As an experienced roofer himself, Cougar said he was dedicated to researching and producing a mag-boot of such outstanding quality that the professional metal roofing industry could, once-and-for-all, overcome the adversity of walking/working on steep slippery metal roofs. He named his new product the Cougar Paws SteelWalker.
While experimenting with the magnetic flux density, Cougar’s first prototypes varied greatly, both by design and manufacturing criteria. Neodymium magnets are one of two types of man-made rare earth magnets. Invented in 1980, these magnets are made up of neodymium, iron and boron and often referred to as NIB magnets. Featured properties of these permanent yet affordable magnets include: very high field strength; increased density of force; and extreme resistance to loss of magnetism. It turns out these are all desirable features for a magnetic boot. Using a magnetic field force meter, I measured the Gauss of each of the eight final NIB-N52 magnets selected for the Cougar Paws SteelWalker model equals. I observed that the average vertical pull force required to release one SteelWalker boot from a steel plate (perpendicular to slope) was 12.5 lb., while a lateral side pull force resulted in a force of only 5.6 lb. This difference can be easily felt on a steel roof, as the lateral side release force is reduced by a 2:1 levering-advantage, with the outside edge of the boot’s sole acting as a fulcrum.
The location of the (4) NIB magnets installed between each boot’s inner and outer soles were changed slightly as the project developed, as was the thickness of the rubber compound overlaying the magnet pockets. Keep in mind that during a dynamic step up slope the forward boot is entirely off the deck momentarily, as the rear boot pushes off. At this instant, the rear boot is momentarily contacting the roof with only the two magnets in the toe, while the heel and instep magnets are raised up, and therefore ineffective. This is the exact point of weakest dynamic magnetic force applied, where the rear boot is most likely to release and slide. The roofer’s mass is then moved vertically over the forward boot, where all four magnets are in contact with the steel, as the rear boot is released and lifted.
Other components that were modified included: the proportional quantities of natural and man-made rubber in the compound formula used in the outsoles; as well as the depth, width and style of the tread patterns necessary to expel moisture under compression, while still providing adequate surface contact area.
After several modifications to the prototype and a final round of static load tests, it was time to add water to the equation. Conducting load tests under wet conditions was particularly challenging, but I finally settled on a quantifiable amount of water adhering to the panels simulating conditions in a light rain.
Test results showed that the majority of boot samples tested over nine months had an average of 24 percent more failures during wet conditions at steeper pitches than compared to dry conditions at the same pitch. The last Cougar Paws SteelWalker prototype tested had a thinner (1 mm) outer rubber covering over the magnets and while the outer sole tread pattern remained the same zig-zag design, the depth and width of the cutouts were increased slightly compared with earlier designs. The boot still maintained a relatively large steel contact area (88 percent) versus the gross area of the outsole. The new design accepted more readily the standing water compressed into the drain channels leading to the gutter around the sole’s perimeter. This new design helped eliminate aquaplaning on steep pitches, common with previous sole patterns.
Acclimation To Mag Boots
According to field test reports by roofers who tried SteelWalkers, it takes a relatively short time to become accustomed to forces caused by their magnetic flux. I began acclimating to their use, by first wearing them one out of four hours on the roof, alternating them with “scuffed” Cougar Paws standard pad boots. My original objective was to ween onto their full use from one hour up to eventually 4-hour periods. After just two hourly shifts in the Cougar Paws SteelWalker boots, I went to continuous wear, as it appeared to me that my brain, nerves and muscles had acclimated to making and breaking boot contact with the metal deck without much, if any disorientation or difficulty. My confidence in Cougar Paws SteelWalker grew as I learned my physical limitations wearing them, and just as with my first pair of original Cougar Paws boots over 10 years ago, stability, balance, agility and reasonable confidence at steeper pitches developed and improved over time.
Corrugated Problems
As my static load test results indicated, the live-load use of Cougar Paws SteelWalker on 3-inch corrugated galvanized-steel roofs proved significantly less effective at and above 10:12 pitch, when compared with galvanized steel roof samples with a flat profile. Therefore, as on any roof, reasonable fall protection and positioning precautions should be employed on a corrugated steel roof.
Like any new professional tool in your gang-box, the boots prove better at some tasks than others. The staggered pattern of the (4) magnets installed in each outsole is best suited when the entire boot load is uniformly applied to the panel. Depending on orientation while standing on a 3-inch corrugated roof panel, the boot’s sole will contact the roof with approximately 35 percent of its total surface area. Likewise, at any one time, only two or three magnets can be centered directly over any steel rib. With fewer effective magnets in use, extra care should be taken to remove any built-up oxidation and iron debris from the boot sole using the supplied cleaning tool. The one-two magnets located over a valley between ribs can be considered non-effective, due to the increased distance between magnet and steel. The field of magnetic flux cannot be insulated or blocked by any known materials. However, it can be deflected by other magnetic fields and objects with higher iron content, entirely nullified by increased distances between surfaces.
During my field evaluations on the 10:12 corrugated galvanized roof on my barn, I immediately observed about a 60 percent reduction in traction, compared with the flat profile of the shallower 4:12 galvanized standing seam on the house. Primarily depending on where I stood on the corrugations, and the angle of the boot sole to the rib line, traction results varied. While the boots provided noticeable aid while working on corrugated panels, I never felt the confidence level produced by flat roofing profiles, such as the standing seam.
Conclusion
I’ve been diligently researching the construction boot market since 1980. When it comes to walking and/or working on steel roofs and floor decking or structural steel, the SteelWalker® magnetic boot by Cougar Paws is the only choice in today’s market that I find worthy of mention.
It’s reasonably priced, and like any construction boot, the Cougar Paws SteelWalker should be considered a consumable item and its cost provided from overhead as a “cost of doing business.” However, if the roofer either uses an inexpensive boot cover or swaps out boots at the bottom of the ladder, the lifetime of the permanent soft outer sole will be greatly extended. Wear them on the steel (never aluminum or composite) sheets for a few days before you make any decisions as to their added value toward your crew’s safety and job profits. Once acclimated to the boot, I’m confident that the comfort, security and productivity of your crews will only increase job after job.
Looking for a reprint of this article?
From high-res PDFs to custom plaques, order your copy today!