Content Is King: Evaluating Decks for Waterproofing Applications
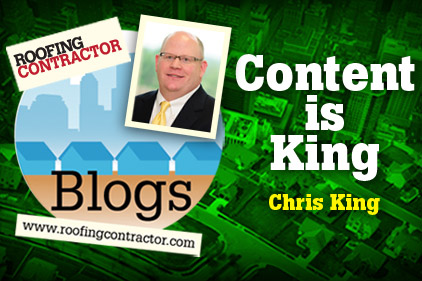
Waterproofing is like playing on the offensive line in football: If you do your job right, no one notices you. If you fail, the result is usually disaster.
At the upcoming International Roofing Expo (IRE) in San Antonio, waterproofing will be the subject of a seminar led by three principals at WJE Engineers and Architects, P.C.: Christopher Giffin, Richard Koziol and Douglas Stieve. Titled “Evaluation of New and Existing Decks for Plaza and Green Roof Waterproofing Systems,” the seminar will be held Thursday, Feb, 7,from7:45 a.m. - 9:15 a.m.
Douglas Stieve gave me a preview of the session and answered some of my questions aboutthe importance of the substrate in the performance of a waterproofing system.
“The substrate or deck of a waterproofing system can be likened to the foundation for a building. It should be robust and stable,” Stieve said. “Most waterproofing systems are intended to last the life of the structure to which they are installed. It is not a system that will be recovered or replaced in 15 to 20 years, like a roofing system might be. Therefore, the substrate needs to be matched with and conducive to the intended service life of the membrane.”
Here’s a portion of the interview:
RC: How can contractors evaluate the suitability of a concrete deck prior to application of the waterproofing system?
DS:The structural components of the deck should be evaluated by a qualified and competent person knowledgeable in structural systems. For new buildings, the deck needs to be dry, sound, and have the proper surface profile for the selected waterproofing system. The moisture content of a concrete deck is one of the most important considerations, and is affected by a number of factors. Some of the more common factors include the type of concrete (lightweight or normal weight) and its initial drying. Construction activities that will occur under the roof deck and the future use of the space under the completed waterproofing system can also allow moisture in the form of vapor to enter the assembly. It is our experience that reliance on number of days after concrete placement as the sole determining factor of when the deck is properly dry can often lead to problems. What happens if there is a significant rainfall on the 25th day after the concrete is placed? For existing buildings, the deck may also need to also be checked for structural defects by a licensed professional, and repaired if there are deteriorated conditions identified or discovered.
RC:Are there different approaches and concerns for new vs. existing decks?
DS:Yes. Existing decks can be much more problematic, as their true conditions are not often revealed until after the existing roofing/waterproofing assembly is removed. Making probes or test cuts as part of the pre-design and pre-construction planning is extremely important and will help limit unpleasant surprises for the owner. Also, having a working knowledge of the type of roof deck and proposed waterproofing system will help a seasoned contractor and/or consultant to be able to anticipate some of the problems that may be encountered. Also, the building code may have requirements that require upgrades, such as drainage enhancements, fire rating and protection improvements, and structural strengthening.
RC: How can contractors and designers determine which waterproofing systems are best for different deck conditions?
DS:There can be many factors that drive decision making for waterproofing membrane product selection, and each and every project will have its own specific considerations. Some common examples are:
• Alterations and/or modifications to building use space.
• Sequencing and scheduling (new and existing buildings).
• Odor concerns during construction.
• Drainage scheme, and any necessary modifications.
• Deck repairs and maintaining watertightness in occupied buildings.
• Type of concrete (i.e., cast-in-place, precast, post-tensioned, composite metal deck form and concrete fill, and either lightweight or normal weight mixes, or cellular concrete).
Typically we prefer a waterproofing membrane over normal weight concrete that is adhered directly to the roof deck as this provides a stable substrate and also aids in chasing leaks if they were to develop in the future. However, if a wet deck is anticipated, a loose laid-membrane with containment grids and relief ports may be a better choice. If excessive deflection and future cracking of the deck is anticipated, a loose-laid membrane may again be a better choice than an adhered membrane that may not be able to accommodate the thermal movements and/or deflections that can influence cracking.
RC:How can contractors determine the moisture content of a concrete deck?
DS:There are several test methods, from pouring hot bitumen on the deck to see if it froths and remains adhered to the deck, taping plastic sheets to the deck to check for condensation, to drilling small probe holes into the concrete deck and measuring the relative humidity. However, other than the bitumen test, there is no consensus or set of guidelines that give roofing contractors a benchmark or “number” to determine what the acceptable moisture content threshold is prior to installing a waterproofing membrane.
RC:What sources of moisture should contractors be aware of after the deck is deemed to be acceptably dry prior to installation of the waterproofing membrane?
DS:The most likely source would be moisture from interior conditioned spaces within the building. If the interior vapor pressure is greater than the exterior vapor pressure interior moisture will be driven up from the interior towards the waterproofing assembly. Further, air infiltration from the interior can also introduce moisture latent air into the waterproofing assembly. Construction activities that may occur within an enclosed building after the waterproofing has been installed can also create tremendous quantities of moisture. Many new buildings are roofed as soon as possible so that the interior trades can perform their work. The moisture generated during interior construction may impact future performance of a waterproofing assembly.
RC:Are there ways to speed up the drying of concrete roof decks?
DS:There are a few ways to speed up the drying by using a lower water-to-cement ratio and not wet curing the concrete. The moisture can also be accommodated if it is anticipated and properly planed for in advance. Vented metal decks can be used to allow moisture to dissipate downward, and vapor retarders can be used in traditional insulated assemblies. There are also moisture blockers that can be applied to the surface of the concrete. For existing decks, there is no real tried and true method. Fans can also be used to move air across the surface of the deck to facilitate drying. The use of a temporary cover or membrane at night that is removed in the day can help with drying but will drive up the cost. We have seen some contractors use torches to dry the outside surface of the deck. However, there likely will still be moisture further down in the concrete that may drive to the surface.
RC:What are some of the most common mistakes made with waterproofing concrete decks?
DS:Probably the most common mistake is not realizing or understanding that moisture exists in the concrete deck. Although the deck may seem dry on the surface, the resulting outward vapor drive will affect most waterproofing systems particularly liquid-applied systems. Another common mistake is the sole reliance on torching the deck surface in attempting to achieve a “dry” condition.
RC:What steps can contractors take to ensure they don’t make those mistakes?
DS:Many contractors are already aware of the steps and checks needed to avoid making mistakes. Good communication and stressing the importance of a thorough check of the deck conditions should be paramount. Becoming more educated on this subject, and networking more with their peers and their professional societies and organizations, like NRCA, RCI and others can be a tremendous help.