Top Ten Air Vent Tips for Roofers From the Field
With Winter Approaching, Roofing Pros Across North America Share their Best Residential Attic Ventilation Tips that have Helped them on the Job
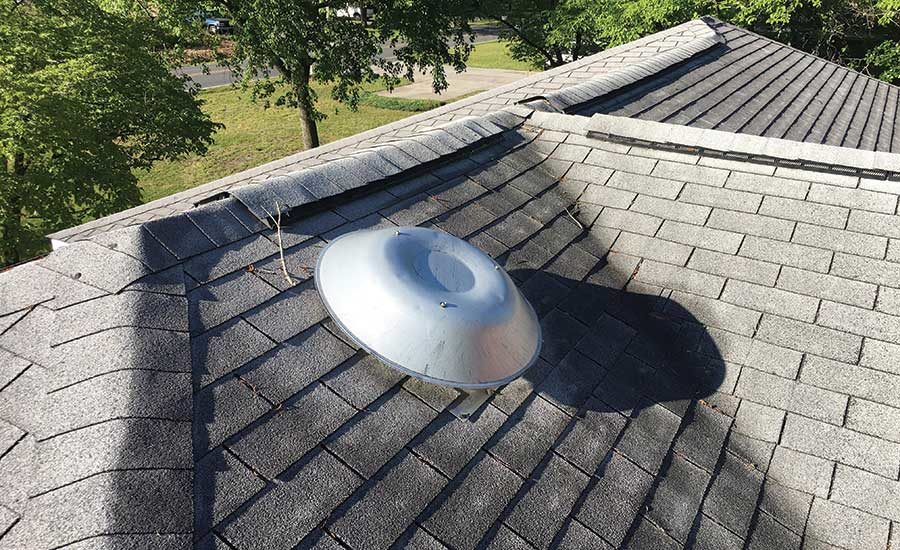
A common mistake is mixing two (or more) different types of attic exhaust vents which can short-circuit the attic ventilation system. Photo by Trevor Atwell.

An attic inspection can confirm whether or not the intake vents are free of any obstructions such as the insulation blocking the airflow. Photo by Ron Bastian.
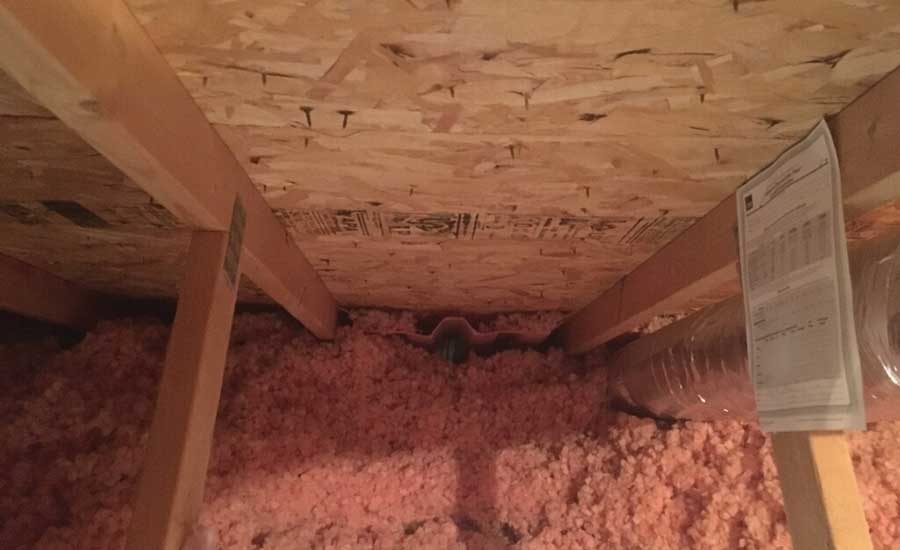
Photos courtesy of Air Vent, Inc.



Who knows better how well (or not so well) a residential attic ventilation system will perform than the actual installer who witnesses the results in person? Who knows exactly which installation methods are highly likely to turn into a problematic callback than the roofing contractor who once was on the receiving end of that callback?
The tips featured here are collected from roofing professionals who generously shared their expertise, best practices and hard-knocks lessons in residential attic ventilation seminars across North America.
1. Keep the Airflow Balanced
“You’re missing the importance of doing a roof right if you’re not addressing all attic ventilation issues, both intake and exhaust,” says Sabrina Johnson, president, KDCO Home Improvement Inc., in Akron, Ohio. “You’re short changing the homeowner and your own integrity.”
That’s why it’s a requirement for Dennison Exterior Solutions & Gutter Topper, of St. Joseph, Mich.
“We require proper attic ventilation (intake and exhaust) to be installed on every project in order for the homeowner to enter into an agreement with our company,” says Scott Dennison, president.
These roofing professionals are firm about the need for balanced attic ventilation because they know firsthand it can help fight heat traps, moisture buildup and ice dams.
“Equal intake with equal exhaust; balanced ventilation is always key,” says Tom Picha, steep slope consultant for Affordable Roofing Inc., in Aurora, Ill.
2. Practice on Your Own Roof
To help convince a homeowner that their new roof needs balanced attic ventilation, Shawn Bellis, owner, EPIC Exteriors in Overland Park, Kan., uses his own house as a learning lab.
“If a contractor practices attic ventilation techniques on their own home they’ll be able to experience for themselves the difference it can make,” he says. Armed with this firsthand information, the roofing contractor is in a stronger position to explain it to a homeowner.
For the record, Bellis thinks intake ventilation is too often overlooked when it comes to balanced attic ventilation (Tip No. 1) so he is constantly reminding his team: intake, intake, intake.
3. Check the Attic
It’s not convenient to go into the customer’s attic to investigate the area. In fact, it’s often hot, dusty and tricky to navigate into and around the attic. Nevertheless, these roofing professionals urge an attic inspection as part of every project when possible.
“You must do a full inspection of each attic,” says Sean Toms, quality control inspector, S & K Roofing in Eldersburg, Md. “Just because you can see fully vented soffit from the outside doesn’t mean there isn’t solid wood underneath. Go into the attic to find out. And while you’re there, look for mold, mildew and condensation marks inside.”
Toms is describing tell-tale signs of moisture problems, which could be properly handled with balanced attic ventilation. But they have to be detected first.
“It’s one thing to look on the outside of the home to check for proper intake but don’t forget to inspect the attic,” says Richard Turner, owner, RJ Turner Remodeling LLC, in High Point, N.C. “Sometimes the intake vents are blocked by the attic insulation or other items and the air can’t flow through correctly.”
“Always check for proper attic ventilation and not just the roof top only (exhaust). Just having vented soffit visible doesn’t equate to a properly functioning attic ventilation system,” says Corey Ballweg, owner and president of Mid Towne Construction of Cross Plains, Wis. “I have seen old wood soffit covered by aluminum or vinyl panels that look like they are letting in plenty of air. More often than not, the installer didn’t remove the wood soffit to an adequate level to allow the newer soffit panels to move the amount of air they are capable of moving.”
Ballweg said he’s also witnessed attic insulation that’s spilled into the soffit, choking the soffit panels from functioning properly.
“This is certainly not readily visible at most attic inspections and may require some roof deck and/or soffit removal to verify the intake air is actually getting in,” he explained.
Still not convinced about the importance of an attic inspection? Talk to Jeff Heitzenrater, owner, Triple Peaks Roofing & Construction, Westlake, Ohio.
“Never, ever take a shortcut by not going into the attic,” he said. “You cannot tell if the attic insulation is in the way of proper intake airflow without scoping it out.”
4. Don’t Mix Exhaust Vent Types
Mixing types of attic exhaust vents is a common mistake and the reason it happens is somewhat understandable: A very demanding homeowner or a misinformed roofing professional thinks “more is better.”
The result can be box vents are added to a roof that already has wind turbines. Or, a power fan being added to a roof that already has ridge vents. Or, ridge vents are added along with the new shingles but the gable louvers (which are exhaust vents) are left open.
“The most common mistake I see, by far, is mixing exhaust vents,” says Jake Jacobson, vice president of SF5 Construction in Little Elm, Texas.
“Never combine sources of attic exhaust. More is not better,” says Trevor Atwell, owner, Atwell Exterior Services LLC, Greenville, N.C.
When two different types of attic exhaust vents (ridge vents, power fans, gable louvers, box vents, wind turbines) are mixed/combined on the same roof above a common attic it could short-circuit the attic ventilation system. This means one of the exhaust types could become the “intake” airflow source. They’re not designed to be intake vents and could bring into the attic not just air but weather. Furthermore, combining exhaust vents reduces the effectiveness of intake vents low on the roof or in the soffit — leaving significant portions of the attic and roof without proper ventilation.
“Short-circuiting is the first tip I would pass along to any home improvement contractor,” said Tim Chapin, owner, Your Safe and Healthy Home, in Akron, Ohio. “We should all be aware if we want to help our clients.”
5. Educate the Homeowner
If the roofing contractor understands the primary benefits of balanced attic ventilation, homeowners will, too, if the contractor takes time to inform them. That’s easier to do if it becomes part of the contractor’s standard operating procedure, says Ron Bastian, owner, Bastian Roofing Inc., in Richfield, Wis.
“Homeowners will benefit both in the summer and winter with proper attic ventilation after you thoroughly teach them why,” he said. “This will set you apart from everyone else bidding on the same project.”
6. Ask Questions
Talking to the homeowner before the project begins helps the roofing contractor better understand the scope of the work to be done. That’s why Jerry Becker, roofing consultant with Roof Life of Oregon, likes to ask questions.
“My favorite question is: ‘So on a hot summer day, does your downstairs tend to be freezing cold but your upstairs is boiling hot? You probably blame it on your HVAC system not being installed correctly, right?’ Just talk to your client and get to know how they live daily in their home. It will help you a tremendous amount.”
7. Wet Spots Don’t Always Mean Leaks
“A good tip I have learned over the years is dark spots on the ceiling are not always a roof leak,” says Sue May, owner, A Better Way Construction & Roofing LLC, in Lincoln, Neb. The trick is explaining this to the homeowner.
May said in the past homeowners assumed all wet ceilings, walls or any other part of the roof area is related to leaking shingles.
“Now we know to look further,” she explained. “Improper attic ventilation is a very common cause of wet areas in the home. If the moist air in the winter cannot exit the attic properly it can condense on the building materials to the point it forms wet spots on the ceilings inside the living space under the attic.”
May’s attic inspections include looking for other moisture-causing trouble spots such as bathroom fans.
“Are the bathroom fans ducted straight into the attic dumping moist air?” she said, noting they should be vented through the roof out of the attic.
8. Keep Attic Temperature Manageable
“Do everything in your power to get the attic temperature within a reasonable range of the outside temperature,” says Paul Vosen, president, Degenhardt Home Improvement, in Madison, Wis.
A homeowner should consider the balanced attic ventilation system working effectively if it can keep the attic temperature within 10-15 degrees of the outside temperature in the summer; 20 degrees max.
Beyond that range we’d want to explore troubleshooting options (R-value of the attic insulation, type and quantity of attic vents installed, etc.). In the winter, the goal is to get the attic temperature as close to the outside temperature as possible to minimize the extreme temperature differentials that contribute to ice dam formation in cold climates.
9. Use Ring Shank Nails
When it comes to fastening attic vents on the roof, the manufacturer’s installation instructions may not specify a specific length or type of nail other than to point out that the nails should penetrate the underside of the deck. Steve DuCharme, owner, Innovative Builders Roofing & Construction, in Edmond, Okla., takes it one step further.
“When installing ridge vents always use a ring shank nail because in windy conditions roofing nails will pull out, especially if the decking is OSB,” he said. Bottom-line tip: be extra mindful of fastening.
10. Never Stop Learning
The final tip doesn’t just apply to the roofing industry because it’s a suggestion that everyone in the skilled trades can benefit.
“Attend a best-practices seminar and always keep learning,” Jacobson said.
Stay on top of your trade the easiest way possible for you: reading industry articles, watching technical videos, participating in professional groups, etc., and by all means, please share your expertise.
Looking for a reprint of this article?
From high-res PDFs to custom plaques, order your copy today!